AC versus
DC
Why does the railroad
industry give such high acclaim to AC traction Systems? Perhaps the simplest way to
answer such a question is to compare the power generating circuits on both DC and AC
locomotives.
|
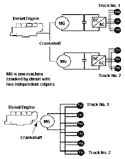 System
schmatic.
|
On conventional DC locomotives, a diesel engine is used to turn a generator. This
generator then produces power which is passed on to traction motors to drive the
wheels. On most of today's existing locomotives, the generator is actually a three
phase AC alternator whose output is internally rectified to DC. This DC power is the
energy used to drive the wheels as mentioned above.
With AC traction locomotives, the same base principle is used. A diesel engine drives
an alternator and the output is rectified to DC. This DC output (referred to as DC
Link) is passed on to inverters which convert the power back into an AC form which
can be used by the AC traction motors. The DC and AC sides of the circuit are in a
sense decoupled by the inverter. This means that operating efficiencies of the
generator and motors can be chosen independently. In other words, the generator can
operate at some certain throttle position at which it is most efficient while the
motors operate at some lower power which is most efficient for them. It is entirely
possible to operate the generator at its maximum 2,600 VDC output while operating the
motors at zero volts. This is the first benefit of AC traction systems. Let's take a
look now at some of the more tangible benefits of AC traction systems.
Nearly all of these advantages are a direct result of the AC traction motor. The
motor used is a squirrel cage, 4 pole, three phase, AC induction motor. The four
poles referred to are magnetic poles. The motor actually has 12 physical poles on the
stator (3 phases per magnetic pole). The advantages gained by using the AC motor are
more pulling power, elimination of stall burns, low maintenance requirements, and the
elimination of short time ratings.
Another advantage to the AC traction system is that an AC induction motor is in a
sense "self-correcting". That is, the wheels will tend not to
slip dramatically. This characteristic is inherent in the concept of an induction
motor. With an induction motor, a magnetic field is set up inside the motor which
rotates at some speed. The rotor will tend to want to "catch up" with this
rotating field. The more the rotor lags behind the field, the harder it gets
"pulled". The more the rotor catches up to the field, the less it gets
pulled. If the rotor actually begins to turn faster than the field, the rotor is
retarded by the field. (This is the case in Dynamic Braking operation.) so, we see
now how the rotor will tend not to exceed the rotation speed of the field. Taking
into account the fact that under most conditions, field frequency does not exceed
rotor frequency by more than 1 Hz, it becomes clear how the induction motor when used
in this system is self-correcting.
A prime example of this characteristic of the motor occurred when one of the prototype
units encountered a slipped motor pinion. The detection software failed to recognize
the faulty motor condition. Since a slipped pinion means that there is no longer a
stable mechanical connection to the axle, the rotor of a DC motor would almost
instantly spin out of control until self-destruction. But with an AC
motor, the rotor will just coast along at the same speed as the rotating field. Since
the maximum continuous speed of the AC motor is 4,000 RPM, and the inverters will not
create a field that rotates faster than 3,600 RPM, the motor is well within its
non-destructive operating range. In fact, when the slipped pinion
happened, it went undetected for more than a day even though system engineers were
riding the locomotive at the time. The software bug that missed detecting this fault
was soon found and corrected.
When a wheel slip occurs on a DC powered locomotive, the main Generator excitation is
reduced in order to reduce the generator output. This reduction limits power into the
slipping motor. The drawback here is that all motors, not just the slipping motor,
see a power reduction. This can be seen easily by looking at the schematic. In order
for power reduction to occur on EMD-built AC locomotives, all wheels
within a truck must encounter slipping conditions! For the unusual case when
simultaneous slips within a truck do occur, power is reduced to motors in that truck
only due to the VSI per truck design of the RADIALAC system. The
other truck continues to work at its non-slipping power level. This can
be seen in the drawing.
Internally, an AC induction traction motor contains no electrical connections for
commutation. Commutation is carried out through the principle of
electro-magnetic induction, as the name suggests. Since no commutators
or brushes exist within the motor, stall burns are no longer possible and short time
ratings have been eliminated. Again, continuous stall condition operation may not be
possible with other manufacturer's locomotives due to fundamental system design
differences.
Lets take this opportunity to clarify the elimination of short time ratings. As with
any electrical machine, these AC traction motors can overheat. However, unlike earlier
motors, these have temperature sensors built into the field windings that provide
feedback into each inverter computer. If the temperature of a motor gets too high,
the inverter computer automatically reduces power to that truck. The operator does not
have to worry about overheating motors on these AC traction units as they will protect
themselves.
How long will the motors run under full tractive effort before the inverter reduces
power to prevent an overheat? This question was answered quite by accident during an
SD60MAC demonstration on Burlington Northern. Three SD60MACs were assembled to pull a
17,000 ton coal train up a steep grade in southern Colorado. Five SD40-2s
normally pull this 30 mile climb at an average speed of 15 MPH. The test consist
reached and consistently held 12 MPH until one of the SD60MACs experienced
difficulties and unloaded. Train speed fell to 6.3 MPG and tractive effort per unit
rose to the maximum of 175,000 pounds. These numbers held for nearly and hour until
the motors approached overheat. The inverters, as expected, automatically reduced
power gracefully, and over the span of 20 additional minutes train speed fell to an
eventual stall only 300 feet short of cresting the grade. What made this exhibition
of producing full (not continuous) tractive effort for such an extended period even
more astonishing is that it happened in 85 degree F ambient air temperature at
roughly 4,000 feet above sea level!
Maintenance requirements on the AC motors are virtually non-existent.
Brush maintenance is no longer required and commutators need not be stoned simply
because the components do not exist in an AC motor. Also, traction motor flashovers
cannot occur, meaning a dramatic reduction in the amount of ground relay trips, hence
less road failures. This means great advantages in high speed operation. The AC motor
is an entirely sealed case with no inspection doors. In fact, visual inspection of the
motor itself, connections in cabling, and gearcase oil level are the only 122 day
maintenance items.
Several factors combine to give an AC motor more "pulling power" than its
DC counterparts. First, an AC motor produces higher starting torques providing
superior performance "out of the hole". Second, AC motors are rated higher
in terms of peak RPM meaning the gear ratio at the bullgear/pinion interface can be
altered to provide higher torques overall without sacrificing ground speed. Finally,
an AC motor can squeeze the same amount of horsepower into a remarkably smaller
package than its DC counterpart. On modern DC units, larger motors occupy much of the
available space in the truck. This makes maintenance of the DC motors difficult. Since
comparable AC motors are smaller in size, higher horsepower can now be achieved with
more reasonably sized motors.
From an operational standpoint, a major variation must be noted under low speed,
heavy pull operation. AC motors on EMD locomotives do not require the high currents
for low speed pulling that a DC motor or other manufacturer's AC locomotives do.
Consequently, much less heat builds in the AC motor on an EMD AC locomotive at low
speeds, virtually eliminating short time ratings. Third, because brushes and
commutators do not exist in an AC motor, stall burns cannot occur. Last, loading
times when moving the reverser from center position to forward or reverse will be
longer as "flux" or magnetism must build up in the motors before operation
can continue. Loading times when changing throttle positions, however, will not be
slower, in fact they may even be faster than on a conventional DC traction
unit.
©
2005 William C. Slim
http://www.okthepk.ca
|