Companion Alternator
Circuits
The Companion Alternator
represents a major departure from past designs. The CA8 still resides within the
housing of the Main Generator, however unlike past applications the stator (output)
windings now produce two separate voltages. One output is 200 VAC @ 900 RPM for Main
Generator field excitation while the other output meets the demand of accessory loads
with 400 VAC @ 900 RPM. The lower voltage level is acquired by "tapping off"
the stator windings at an appropriate location.
Accessories driven by the CA8 include:
- 2 speed Traction Converter Cabinet Blower Motor
- Phase Module internal Pre-heaters
- 3 speed Traction Motor Blower Motors (8 x engine speed in DB for fuel
savings)
- 1 speed MG/CA housing Blower and #1 Inertial Blower Motor
- 2 speed Radiator Blower Motors with 52 inch fans
- 2 speed Air Compressor Motor
A great number of devices require power from the CA8 to operate. Due to loading
limits, the CA cannot handle the transition from OFF to ON/LOW to HIGH of more than
one load at a time. For this reason, a set of current transformers has been installed
on the accessory load output of the CA for determining when a particular load has
completed its transition stage. Upon completion according to CT feedbacks, EM 2000
allows transition of the next device of highest priority. Installation of these
transformers also enables EM 2000 to determine if a particular load is failed either
shorted or open. For example, when allowing a device to make transition to a higher
power consumption state, EM 2000 expects to see CT feedback rise very high momentarily
before stabilizing at some moderately high level. If feedback does not rise, this
signifies an open power path to/through that device. Likewise, if CT feedback surges
very high then fails to moderate, this represents a short circuit in the power path
to/through that device.
As with past locomotives, the CA provides output to a set of silicon controlled
rectifiers (SCRs) which regulate the amount of current passed to the main Generator
field windings. Additionally, as in the past, the Main Generator is actually two
separate electrical alternators (stator) within a single housing excited by a common
field (rotor). However, as explained later in this text, the two machines are for the
first time entirely independent of one another.
DC Link Capacitor Discharge
Some safety precautions pertaining to work with high voltage systems must be
covered. Unlike the high voltage circuits implemented on conventional DC traction
locomotives, the AC traction system design requires elements to store energy in the
form of high voltage. These circuit elements are referred to as DC Link Capacitors.
In order to ensure safe working conditions, proper procedures for discharging these
elements must be followed.
As the inverters employed in the traction system on this locomotive are of the
Voltage Source type, capacitors connect in parallel with the load (inverter) and
source (Main Generator) to provide a constant voltage supply at the load. Several
"cannon type" * capacitors in the locomotive's high voltage circuit form a
storage bank for energy. This bank has the capability of storing a fault condition DC
Link overvoltage charge of 3,600 VDC, though the nominal charge does not exceed 2,600
VDC. For the purpose of protecting equipment as well as personnel, several automatic
discharge systems operate on this unit. These systems are described briefly here.
* The term "cannon type" refers to the fact that each capacitor is roughly
the diameter of a coffee can and approximately 3 feet in length, making it resemble
the barrel of a cannon.
Automatic discharge capabilities are built into the inverter system with redundancy.
The first discharge path is through a set of high impedance resistors which act to
constantly "bleed" charge off the capacitors. For this reason, these
elements are commonly referred to as "bleeder resistors". The presence of
these resistors makes the maximum discharge time from any voltage level 1 minute.
A second path for discharge is through the Dynamic Brake resistor grids. These
connect across the capacitors any time the Isolation Switch is placed in the ISOLATE
position. The only requirement for this action to apply is that battery voltage be
present; computer systems do not need to be operational!
A third action for discharge takes place any time the diesel engine stops turning.
When this happens, the Auxiliary Generator stops turning and ceases to produce
output. A critical subsystem within the inverter requires Auxiliary Generator supply
to properly function, therefore if Aux. Gen. input is lost, the inverter triggers an
electrical "crowbar". The crowbar creates what is essentially a direct
short circuit across the capacitors which discharges them instantly. This action
actually results in a total of four discharge paths since the triggering of one
crowbar causes the triggering of an additional three.
After any of the previously stated automatic discharge methods lower DC Link
Capacitor voltage to a level of less than 50 VDC, the switch gear motors into position
to short out the entire high voltage system and tie it to ground through the Ground
Fault detection circuitry.
Remember that every operation detailed occurs automatically, and that any of the
operations alone is sufficient to discharge the system!
To be certain that the automatic discharge methods have achieved their end goal, a
system self test may be executed by use of the display. If this self test determines
that high voltage has not been removed, the user is notified via computer display
messages and the sounding of an alarm.
Electrical Crowbar
|
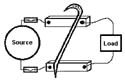 Electrical
crowbar.
|
The purpose of an electrical crowbar device is to protect both the load and supply
from potentially damaging overvoltage and overcurrent conditions. To do this,
obviously current and voltage must be monitored. If those monitored values exceed
values set by software or hardware, then protection is activated which intentionally
short circuits the source. How does this function make the device similar to a
"steel" crowbar? Consider the circuit as shown. When protection is
activated, the "steel" crowbar is dropped across the bus bars creating a
dead short circuit of the source. Obviously, this would trip the circuit breaker
rather hastily.
As mentioned before, two methods of protection (either a "hard" or a
"soft" crowbar) can be initiated. The hard crowbar creates an authentic
short circuit of the source with virtually zero resistance. The soft crowbar performs
the same action, but with a resistance in series of approximately 3 Ohms. This
resistance is the IPR (Inverter Protection Resistor). In both cases, the EM 2000 is
instantly notified of the crowbar firing, and Main Generator excitation is shut down.
The signal that a crowbar has fired can either come via serial link or be detected
directly by EM 2000 DC Link current feedback signals. The serial link signal, DC Link
Current feedbacks, and EM 2000 collectively make up the "circuit breaker" in
this high power circuit. In any case, since generator excitation ceases, the output
will rapidly decay through the crowbar and protect the traction system from further
damage potential.
©
2005 William C. Slim
carknocker@okthewp.ca http://www.okthepk.ca
|